ボルトの外観検査は、ボルトの製造工程で品質を保証する工程のひとつです。ボルトは製品や建築物などで使用され、締結したい対象物を固定する役割を果たす部品です。そのため、締結できない、締結力が足りないとなると固定が安定せずに、商品の不良や建設物の安全性などの問題が発生します。そこで本記事ではボルトの基礎の復習から、ボルトを外観検査する際の確認項目や検査基準などについて説明をしていきます。さらに目視での外観検査と画像での自動外観検査の比較についても言及していますので、目視と画像でどのようなメリット・デメリットがあるかを把握してみてください。ボルトの外観検査について知識を深めて、適切な外観検査の方法を検討していきましょう。
ボルトの外観検査の目的
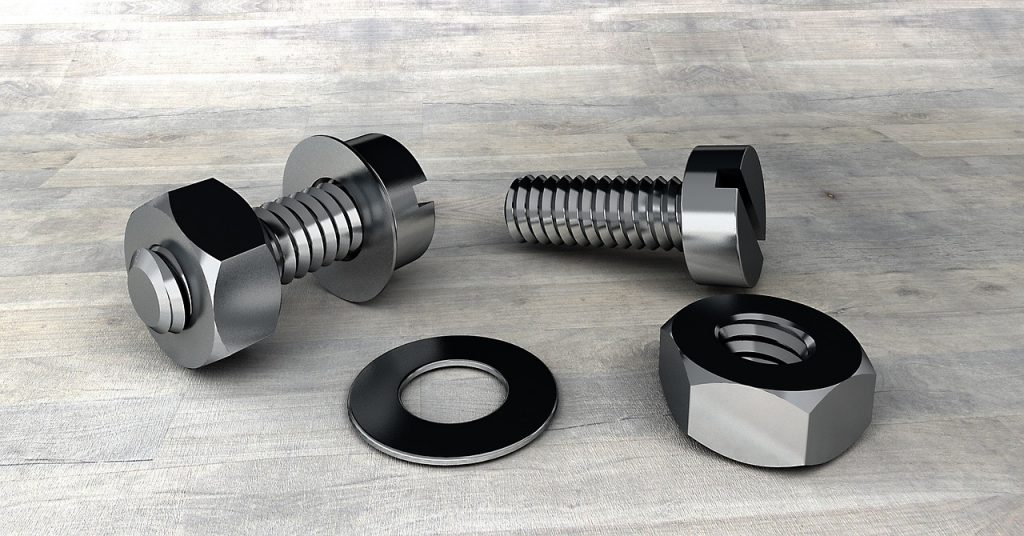
ボルトの外観検査は、製品の品質を確保するために重要です。この検査は、製造過程や取り扱いによって生じる潜在的な欠陥や劣化を早期に発見し、製品の品質を確保するために行われます。ボルトは機械部品の一部であり、適切な強度や寸法精度が求められるため、外観検査は欠陥の有無や寸法の適合性を確認するために欠かせません。
外観検査では、ボルト表面に生じる傷やへこみ、錆、塗装の剥がれなどの欠陥を視覚的に確認します。これらの欠陥が存在すると、ボルトの強度や耐久性が低下し、使用中に破損や事故の原因となる可能性があります。また、寸法精度も検査対象となり、ネジ山の形状や直径、長さなどが規格に適合しているかどうかを確認します。外観検査は目視で行われることが一般的ですが、一部の欠陥は肉眼では確認しづらい場合があります。そのため、顕微鏡や拡大鏡を使用して検査を行うこともあります。
ボルトの基本知識
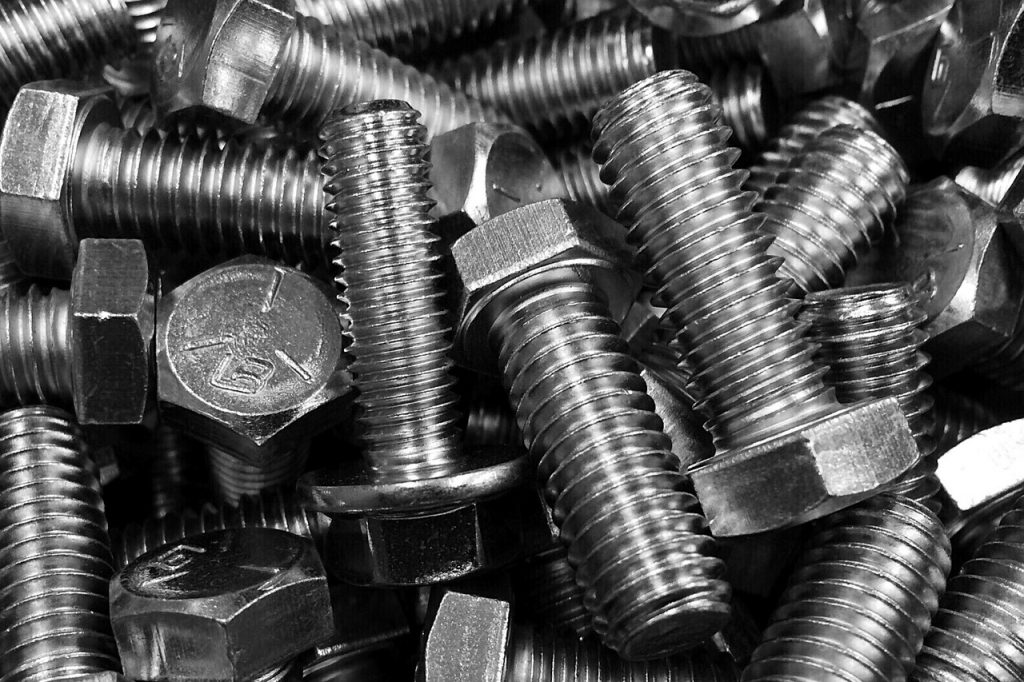
ボルトは雌ネジがないと締結できないネジの一種です。ここでは一度ボルトの基本知識についておさらいします。
ボルトの各部名称
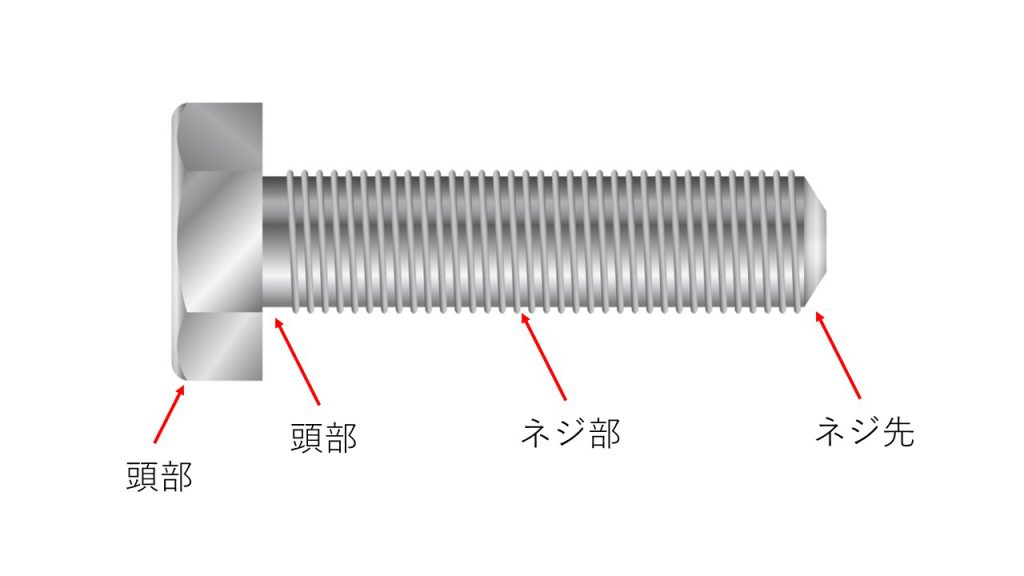
ボルト各部の名称について説明します。
頭部
ボルトの一端に位置し、ネジが締め込まれすぎないように固定する役割があります。また、レンチやドライバーで回すための溝はリセスと呼びます。頭部の形状には六角や六角穴付きなど種類がありますが、これらの溝や頭部の形状によって、使用される工具や締め付け方が異なります。
本体部
頭部とねじ部をつなぐ部分で、ほぼ円筒形状をしています。強度を保つために、適切な直径と長さが重要です。
ネジ部
ボルトの本体部に切られた螺旋状の部分形状で、ネジの機能を果たす重要な部分となります。他の部品に取り付ける際に使用されるため、ねじ山の形状やピッチが正確であることが重要です。
ネジ先
ボルトの先端に位置し、他の部品に取り付ける際に先導役として役立ちます。平先が一般的な形状になりますが、他にも用途によっていくつか種類があります。
ボルトの締結構造
ボルトの締結の仕組みについて説明します。まず、ナット(雌ネジ)を回して、ボルト(雄ネジ)と被締結物に圧縮力をかけることで、ボルトに引張力(締結物の反発力)が発生します。この発生した反発力が、ボルトとナットの締め付け座面やお互いのネジの接触面の摩擦抵抗と相まって被締結物が固定されます。これらが、ボルト締結の仕組みになります。
したがって、ボルトの締結には、いくつかの要素があります。まず、ボルトとナットの組み合わせが重要です。これらは、互いに適合する必要があります。また、正しいトルク(ねじりの強さ)をかけるために、適切な工具(トルクレンチなど)を使用することも重要です。適切なトルクをかけることで、締結が正しく行われ、ボルトが緩んだり、破損したりすることを防ぐことができます。
ボルトの締結は、安全性を確保するために非常に重要です。ボルトの形状や寸法が設計した条件に合格していないと、締結物が緩んだり、崩れたりする可能性があります。そのため、ボルト製造における外観検査は大切な工程となります。
ボルトの製造工程
ボルトの製造工程は複数にわたりますが、基本的な流れは以下の通りです。
ブランク形成
ブランク形成では、鋼材料を所定の形状に加工し、ボルトの原料となるブランクを作ります。一般的な方法としては、鋼材を熱間鍛造や冷間鍛造、切削加工などによって加工し、ボルトの形状に近い形状に加工します。この工程で、ボルトの基本的な形状が作られます。
ネジ形成
ネジ形成工程では、ブランクから作られた基本的な形状を持つ部品に対して、ネジを形成する加工が行われます。一般的には、旋盤加工やロール加工などの方法が使われ、部品の表面にネジ山を形成します。この工程で、ボルトのネジ部分が完成します。
熱処理・表面処理
ボルトの強度や耐久性を向上させるために、熱処理や表面処理が行われます。熱処理では、ボルトを一定の温度に加熱し、冷却することで組織を微細化させ、強度を向上させます。表面処理では、ボルト表面に皮膜を形成することで耐食性や摩耗抵抗性を向上させます。
ボルト外観検査の確認項目
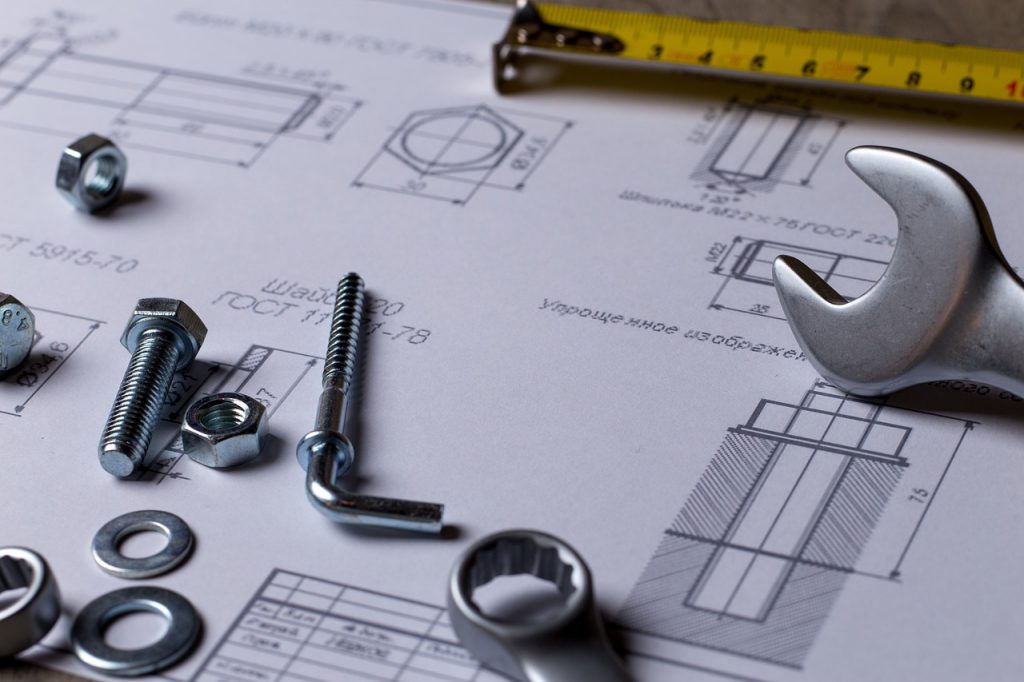
ボルトの外観検査では、以下のような項目を確認します。これらの項目の確認は、ボルトの製造や取り扱い過程で生じる潜在的な問題を早期に発見し、製品の品質を確保するために重要です。
切り忘れ・加工ズレ
切り忘れや加工ズレがないかを確認します。これらの欠陥があると、ボルトの正確な寸法や形状が得られず、組み立て時に問題が生じる可能性があります。特に加工ズレがあると、ボルトの強度や取り付け時の安定性が損なわれるため、検査が重要です。
破損(割れ・欠け)
ボルトに破損(割れや欠け)があると、その部分が弱点となり、使用中に破損する危険性があります。検査ではボルト全体を丁寧に観察し、破損部分がないかを確認します。
バリ
バリとは、加工過程で生じる鋭利な突起のことです。ボルトにバリがあると、他の部品との組み合わせや取り付け時に問題が生じる可能性があります。外観検査では、ボルトの表面を注意深く確認し、バリがないかを確認します。
異物混入
異物混入は、ボルト内部や表面に異物が混入している状態を指します。異物が混入すると、ボルトの性能が低下し、取り付け時に問題が生じる可能性があります。検査では、ボルトの表面や内部を観察し、異物が混入していないかを確認します。
寸法検査
ボルトの寸法は、正確である必要があります。寸法が規格外の場合、他の部品との組み合わせや取り付け時に問題が生じる可能性があります。検査では、ボルトの長さや直径などの寸法を測定し、規格に適合しているかを確認します。
ゲージ検査
ゲージを使用して、ボルトのネジ山や寸法などを精密に検査します。ゲージ検査は、目視検査だけでは確認しづらい微細な欠陥や寸法のずれを検出するために行われます。
ボルトの外観検査を目視で行う問題点
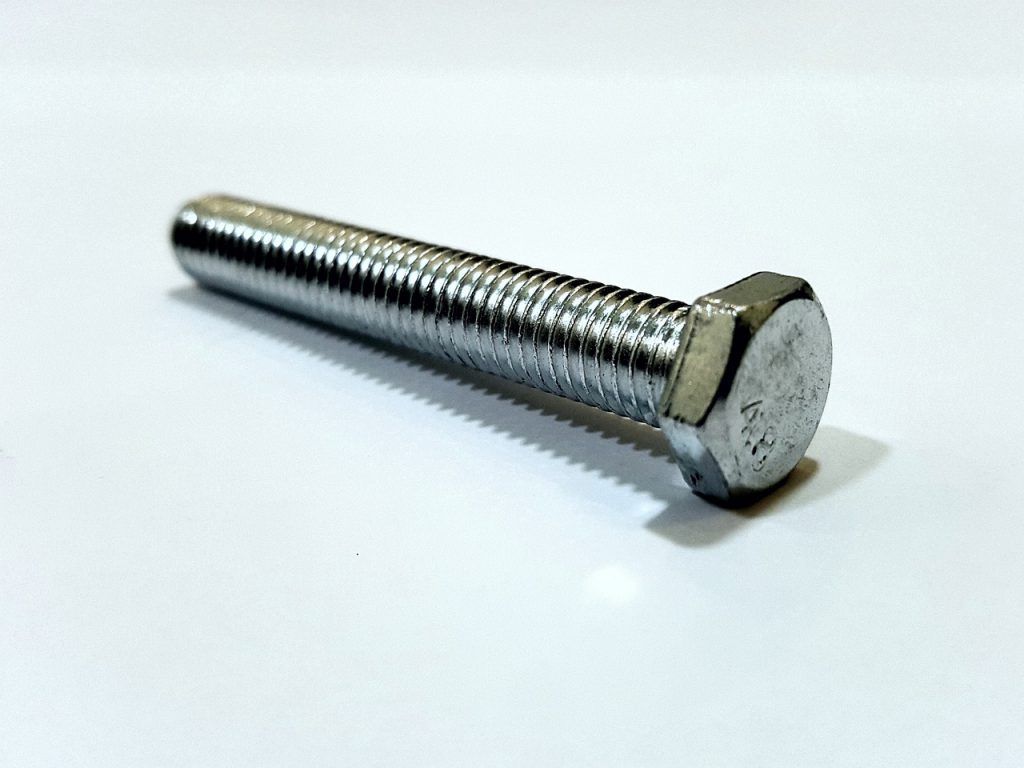
ボルトの外観検査を目視で行う際には、以下のような問題点があります。
検査時間がかかる
目視検査は作業者が一つ一つ確認するため、大量のボルトを検査するのに時間がかかります。特に精密な検査を行う場合は、検査時間がさらに増加します。このため、効率的な検査方法が求められます。
検査精度が低い
人間の目視による検査では、細かい傷や欠陥を見逃す可能性があります。また、作業者によって検査の基準が異なることも精度を低下させる要因となります。検査精度を向上させるためには、より厳密な基準や検査手法が必要です。
検査コストがかかる
目視検査は作業者の労力が必要となるため、検査コストが高くなる傾向があります。また、人間による検査ではミスが発生する可能性もあるため、再検査や不良品の取り扱いにもコストがかかります。
ボルトの外観検査は画像検査で自動化
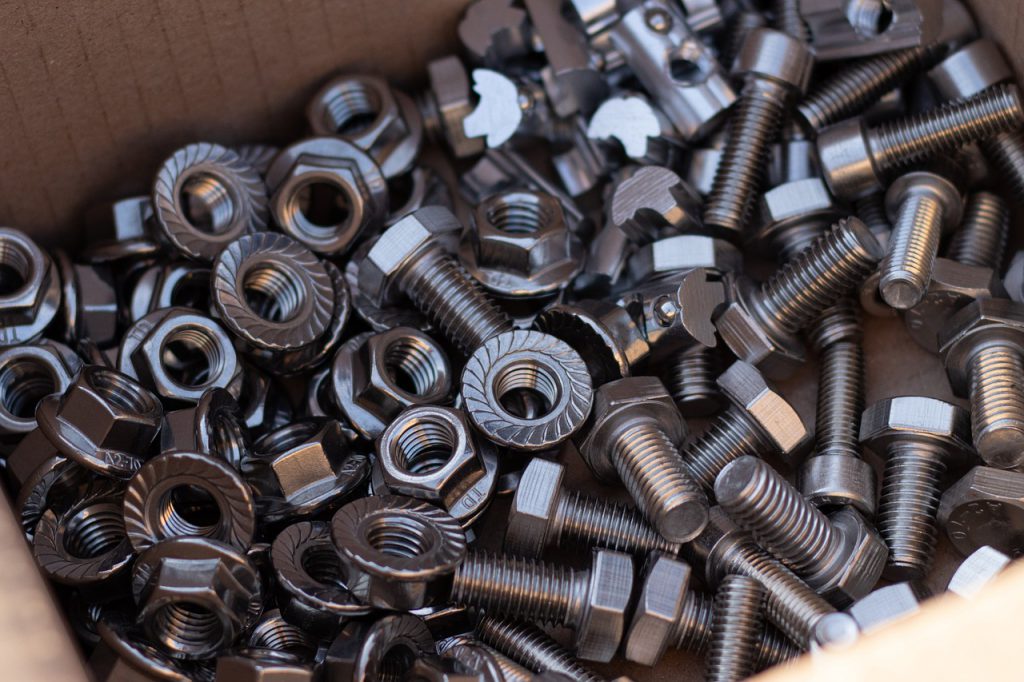
ボルトの外観検査は、従来は目視で行われることが一般的でしたが、近年では画像検査技術を用いて自動化されることが増えてきています。画像検査を用いることで、検査時間の短縮や検査精度の向上、検査コストの削減が期待されます。
検査時間の短縮
画像検査では、カメラやセンサーを用いてボルトの外観を高速で撮影し、画像処理技術を用いて欠陥や異常を検出します。このため、従来の目視検査に比べて検査時間を大幅に短縮することが可能です。
検査精度の向上
画像検査では、画像処理技術を用いて微細な欠陥や異常を検出することができます。人間の目では見逃しがちな細かい欠陥も確実に検出することができるため、検査精度の向上が期待されます。
検査コストの削減
画像検査を導入することで、人件費や再検査のコストなどを削減することができます。また、自動化によって検査の一貫性や効率も向上させることができます。
Phoxter の画像処理システムでより効率的なボルトの外観検査を実現
Phoxterの画像処理システムを活用することで、更にボルトの外観自動検査の効率化を目指すことができます。ここではPhoxter画像処理システムの特徴をご紹介します。
ハードウェアの拡張で最適な機能の設定が可能
従来の画像処理システムは、検査する内容により機器の構成の変更が必要でした。そのため、追加の検査項目があると、後で機材を追加しなけらばならない問題を抱えていました。しかし、Phoxterの画像処理システムでは、共通のハードウェアに対してその筐体の中身のみを拡張することで検査項目の変更や追加に対応することが可能となります。
複数の検査項目を1度の測定で判定が可能
Phoxter画像処理システムを活用すれば、ボルトの外観検査で検査しなければならない複数の項目を一度の測定で判定することが可能です。検査項目によって使用していた顕微鏡やノギス、ゲージなどの機器も画像処理システムによって必要なくなるメリットがあります。
過検知の問題をAIで解決
従来の画像検査では精度の高い検査基準を設けることが難しく、検査の閾値を過度に安全サイドに設定して検査をしなくてはいけない課題がありました。この過検知による無駄の問題をPhxterの画像処理システムの持つAI画像処理機能によって解消することができます。
母材やマシンの刃面の影響をうけない外観検査が可能
ボルトの母材が変わる、あるいは、カッターのチッピングなどで表面性状が大きく変わった良品画像が得られるケースがあります。このような場合でも、AI検査ならば非常に安定した検査結果を担保できます。PhoxterのStellaController2.0なら、ワークサイズに適応する焦点自動変更のレンズと組み合わせて1カメラで複数サイズのワークへの対応も可能ですので、コスト低減が可能です。
まとめ
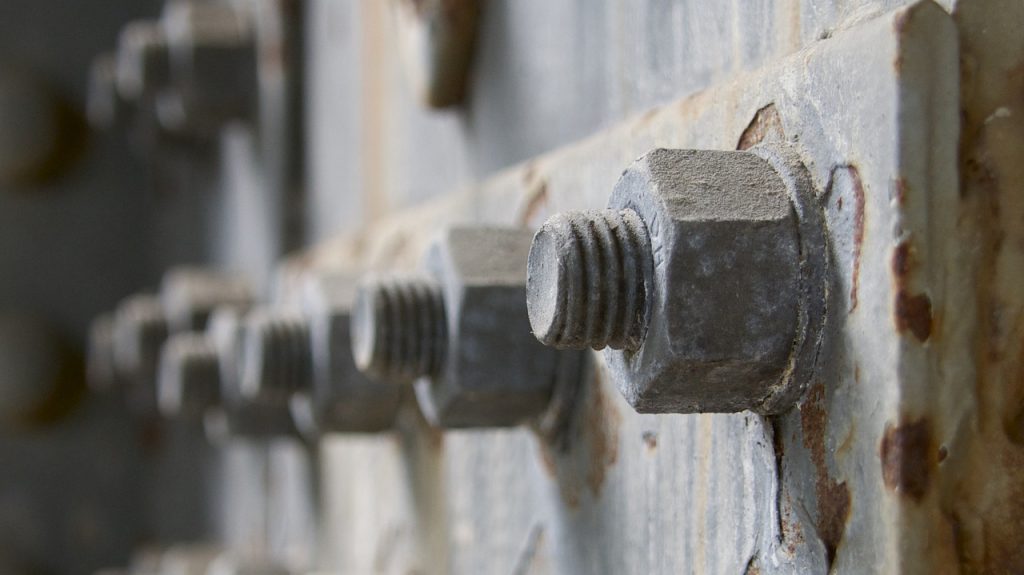
ボルトの外観検査はボルト製造の工程において欠かせないプロセスです。まず、ボルトの機能や構造を理解することが、検査で不具合を見落とさないポイントとなります。また、具体的なボルトの外観検査の検査項目を抑えながら検査をしていくことが重要になります。
ボルトの外観検査が目視での検査が一般的ですが、検査時間が長くなってしまったり、作業員の検査能力のばらつきによる精度不足など、総合して検査コストがかかってしまうというデメリットがあります。そこで、近年では画像測定器による画像検査の導入も増えてきている状況です。一方で、画像測定器を導入してボルトの外観検査を始めるといっても、知識が足りずなかなか導入に踏み切れないのも現実です。
Phoxterでは外観検査の自動化を推進するためのソリューションをご提案する中で、画像測定器の選定から費用対効果のご提案などができる体制を用意しております。ボルトの外観検査における適切な画像測定器や設備の設計など、お困りごとがありましたらぜひPhoxterまでお問合せ下さい。