工場や物流現場での効率化を図る際、多くの方が頭を悩ませるのが「どうやって自動化を進めるか」という課題です。そんな中で注目されているのがAGV(無人搬送車)やAMR(自律移動ロボット)の活用です。これらの技術を上手に活用することで、作業効率の向上や人手不足の解消を図ることが可能です。しかし、AGVとAMRの違いや、それぞれの活用事例を理解することは容易ではありません。この「工場や物流現場でのAGV・AMR活用事例」では、AGVの基本理解から活用事例までを詳しく紹介しています。特に、幅広い様々な観点での活用事例を紹介することで、AGV/AMRの活用による生産性向上のヒントを得られることでしょう。
AGV/AMRの基本理解
AGVの定義と歴史・無人搬送車の基礎知識
AGV(Automated Guided Vehicle)は、自動化されたガイド付き車両として、工場や倉庫内での搬送作業を効率化するために使用される無人搬送車です。初めてAGVが登場したのは1950年代のアメリカで、工場内の物資輸送を自動化する目的で開発されました。初期のAGVは、磁気テープなどの誘導体を用いて決められた経路を走行するシステムが中心でしたが、技術の進化に伴い、現在ではレーザー誘導やGPSを用いるものも一般的になっています。
AGVとAMRの違い
AGV(Automated Guided Vehicle)とAMR(Autonomous Mobile Robot)は、どちらも自動化された搬送システムとして注目されていますが、その動作原理や適用範囲において大きな違いがあります。AGVは主に固定された経路に沿って動作する無人搬送車で、床に設置された磁気テープやレーザーガイドを利用して移動します。これにより、搬送経路が明確であるため、安定した動作が可能ですが、経路変更には構造的な変更が必要となり、柔軟性に欠ける一面があります。
一方、AMRは環境をリアルタイムで認識し、自律的に最適な経路を選択して移動することができるロボットです。センサーやカメラを用いて周囲の状況を把握し、障害物を避けながら効率的に動くことができるため、動的な環境変化にも対応可能です。このため、AMRは柔軟性が高く、頻繁なレイアウト変更が行われる環境に適しています。
AGVとAMRは、どちらも自動化された搬送を実現するためのテクノロジーであり、労働力の補完や生産性の向上を目的として導入されるなど共通点も多いため、正確な定義の違いが意識されずに用いられるケースも数多く見受けられます。本記事で紹介する活用事例においても、「搬送の自動化」という点に着目し、「AGV/AMR」と記載する点をご了承ください。
AGVとAMRの違いの詳細については、こちらの記事「AGV(無人搬送車)とAMR(自律走行搬送ロボット)を徹底比較!」でご紹介しています。
工場・倉庫におけるAGV/AMR活用事例
エリア別分類
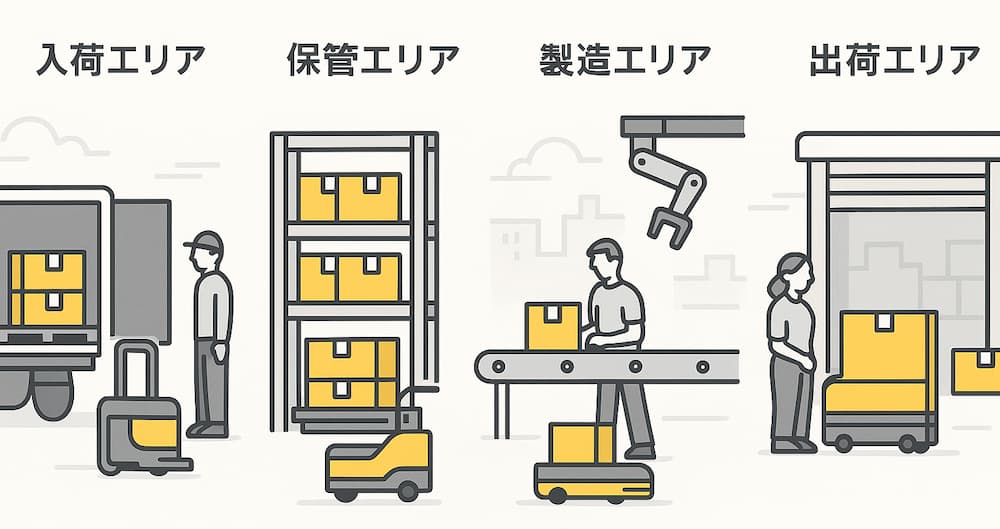
入荷エリア
工場や物流施設では、トラックで運ばれてきた荷物を受け取る入荷エリアでAGV/AMRが活躍します。パレット単位での荷下ろし後、自動的に検品エリアや保管エリアへ搬送。人手を介さずスムーズに荷物を流すことで、荷役の省力化とトラックの滞在時間短縮が図れます。
保管エリア(倉庫/保管棚周辺)
倉庫や中間保管エリアでは、AGV/AMRが棚搬送や補充作業を担います。棚間の移動が頻繁なエリアで、定位置への正確な搬送が求められるため、高精度なナビゲーション機能が活かされます。温度帯が異なるエリア間の搬送や、WMSとの連携による在庫管理も可能です。
製造エリア(工場内ライン)
製造工程では、部品供給や仕掛品の工程間搬送などでAGV/AMRが利用されます。組立や加工のタイミングに合わせてJIT(ジャスト・イン・タイム)搬送を行うことで、ラインの停止を防止。MESと連動させてトレーサビリティの確保や、混流生産対応も実現できます。
出荷エリア
出荷エリアでは、完成品を梱包・検査後に出荷バッファまで自動搬送し、ドックへの積み込みを支援します。作業員が重量物を長距離運ぶ必要がなくなり、負担軽減やヒューマンエラー防止にも効果的。ピーク時の出荷処理もフレキシブルに対応可能です。
搬送対象別分類
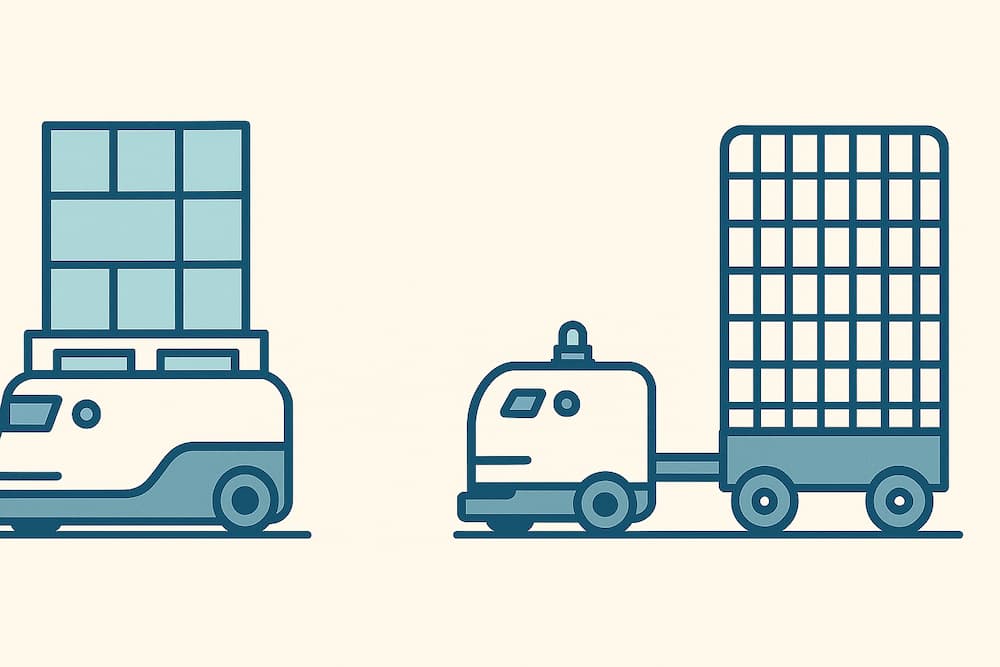
パレット単位
重量物を搭載できる大型AGVが使用され、入出荷エリアや保管棚間の搬送に最適です。パレット積載された製品や資材をそのままの形でトラックから倉庫内へ搬送したり、工程間を横断的に移動させるなど、人手では困難な重量作業を自動化します。
カゴ台車単位
物流倉庫やECセンターなどで多く使われ、AGV/AMRに台車をけん引または載せ替えて搬送します。ピッキング後の商品や仕分け済みの荷物を複数拠点に分配搬送する用途で利用されるなど、柔軟なルート設計と安全制御が求められます。
通い箱(コンテナ)
生産ラインや部品供給エリアで活用されます。トレイやボックスに分類された部品・材料を工程ごとに分配搬送し、JIT生産や多品種少量生産にも対応可能です。棚搬送型AGV/AMRやリフト式AGV/AMRと組み合わせて使われることも多いです。
ケース単位(ダンボール)
製品梱包後の搬送や、通販・出荷工程でよく使われます。軽量なケースでも数が多くなると作業者の負担が大きくなるため、AGV/AMRがピッキング棚前まで搬送、作業者が積載した後、出荷ラインまで自動搬送するなどの省力化が進んでいます。
仕掛品(部品トレイ、治具ごと)
製造ライン間での工程間搬送において、未完成品(WIP)のトレイや治具をそのまま搬送する用途です。治具付きでも位置ズレを起こさない高精度な停止制御が必要となり、搬送履歴のトレーサビリティも重要視されます。
小物部品のピース単位
1個単位の部品を搬送するケースでは、棚搬送型のAGV/AMRが活躍します。棚ごと作業者のもとに届ける「Goods-to-Person方式」や、ピッキングステーション間の自動搬送などにより、人的移動を削減し生産性を向上させることができます。
運行方式別分類
定期巡回型
あらかじめ設定されたルートを一定間隔で巡回する方式です。定期的な部品供給やゴミ回収、空容器回収など、ルーチン業務に最適。設備側との連携不要で導入も簡易で、ライン稼働の安定化に貢献します。
オーダー都度搬送型(呼び出し対応)
設備や作業者からの要求に応じてAGV/AMRが都度搬送を実施する方式。MESやWMSからの指示と連動することで、タイムリーかつ柔軟な搬送が可能です。多品種少量の現場に適しています。
合流・分岐制御型(交差点制御あり)
複数の搬送ルートが交差する環境で、センサーや交通制御システムにより安全に合流・分岐を行う方式。混雑や衝突を回避しながら複数台が効率的に走行でき、工場・倉庫全体の搬送最適化に寄与します。
トレーサビリティ管理連動搬送
搬送対象物に個別ID(RFID、バーコードなど)を付け、AGV/AMRの搬送経路や履歴をすべて記録。製造記録や出荷履歴の整合性が求められる業種に適しており、品質保証や監査対応にも有効です。
複数台連携フリート制御(群制御)
複数台のAGV/AMRを中央管理システムで統合制御し、搬送需要に応じて最適な機体を割り当て。リアルタイムで状況を監視しながら走行スケジュールを自動調整することで、最大効率を発揮します。
ダイナミックスケジューリング型(混雑回避)
リアルタイムの稼働状況や通路の混雑状況をもとに、AGV/AMRが自律的にルート変更や順序調整を行う方式。複雑な環境でもボトルネックを回避し、運用の柔軟性と安定性を両立します。
連携システム別分類
MES(製造実行システム)と連携
生産計画や実績と連動して、必要な部品や仕掛品を適切なタイミングで搬送。ラインの稼働状況に応じた柔軟な対応が可能となり、製造の効率化とトレーサビリティ強化に寄与します。
WMS(倉庫管理システム)と連携
在庫情報や棚番情報を基に、保管場所からの搬送や格納指示を自動化。入出庫業務を最適化し、人的ミスの削減やリードタイム短縮が図れます。棚搬送型AGV/AMRとの相性も良好です。
ERPとの在庫連携
企業全体の在庫・購買管理と搬送業務を統合。調達タイミングや出荷状況に応じてAGV/AMRを制御することで、サプライチェーン全体の可視化と自動化が可能となります。
自動倉庫・自動棚との連携
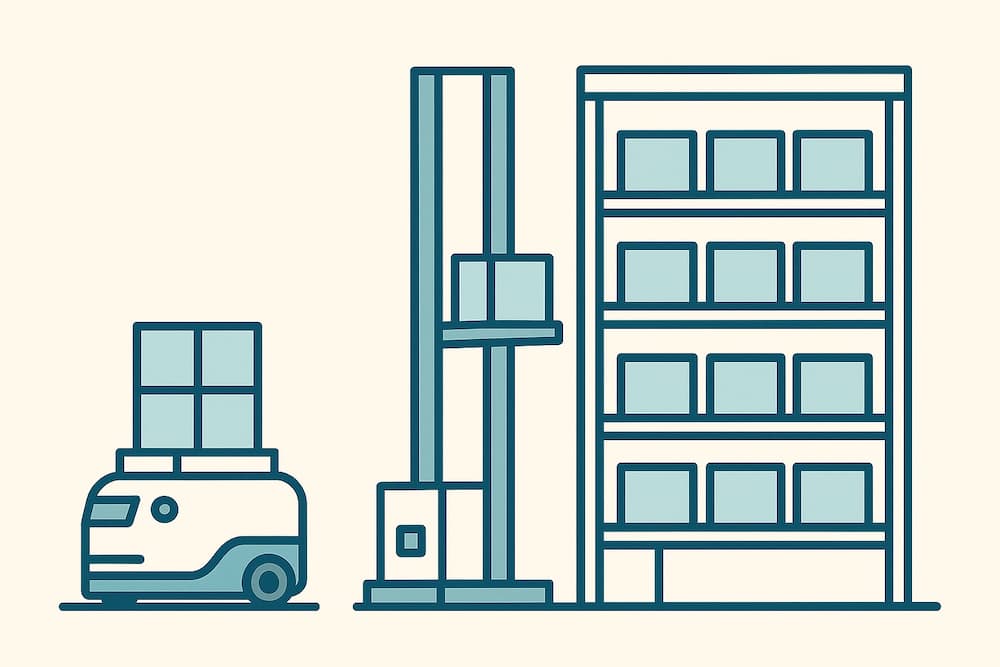
スタッカークレーンや自動昇降棚などの保管設備と連動し、取り出し位置や格納位置を自動で搬送。WMSと合わせて使用することで、無人に近い保管搬送ラインを構築できます。
ロボットアームとの協調搬送
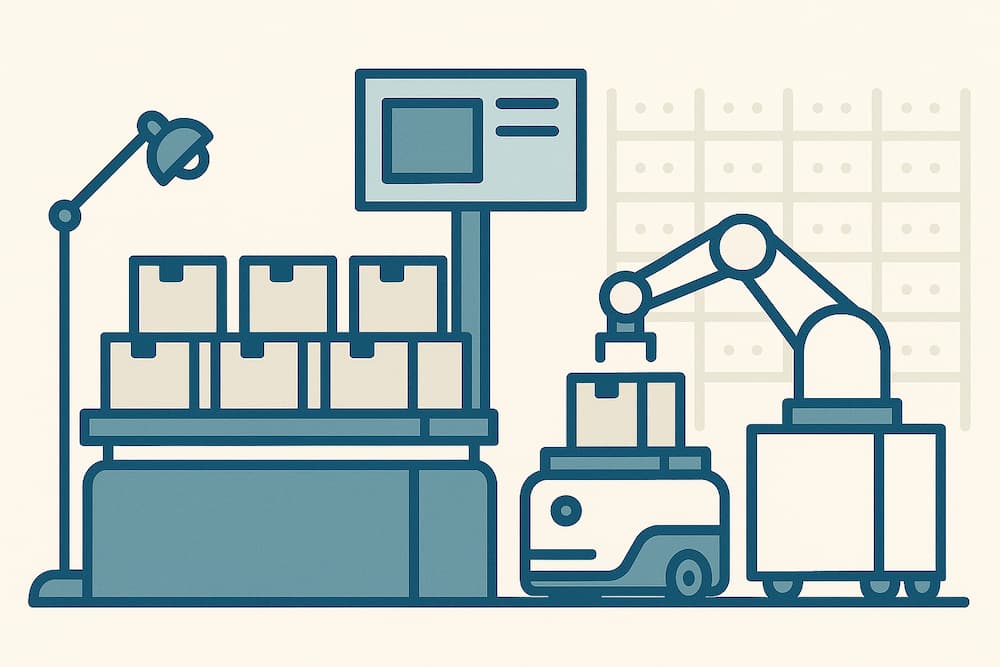
AGV/AMRがロボットアームの前まで物品を搬送し、受け渡しや配置を自動で実行。無人化工程や組立セル内での物品供給に活用され、完全自動化に近づける構成が可能です。
検査装置との連携(検査後の自動搬送)
画像検査機や寸法測定装置と連携し、不良品・良品の振り分け後に自動で次工程へ搬送。ヒューマンエラーの排除や品質トレーサビリティの強化に繋がります。
ピッキング支援システム(DPS等)との統合
デジタルピッキングシステム(DPS)やライトピッキングシステムと連動し、指示に従ってAGV/AMRが棚やケースを運搬。作業者のミスを減らし、ピッキング作業の効率を大きく向上させます。
物理環境・構造条件別
フラット床・段差なし
標準的なAGV/AMRが最も効率を発揮する環境。ガイドレスでもスムーズに移動でき、センサーやマーカーの設置も最小限。大規模な倉庫や製造ラインでの搬送に最適です。
スロープ・段差あり環境
段差や傾斜が存在する現場では、登坂性能や自動制動機能を備えたモデルが必要。走行安定性を保ちつつ、荷崩れ防止などの安全対策も考慮されます。
エレベーター連携(階層移動)
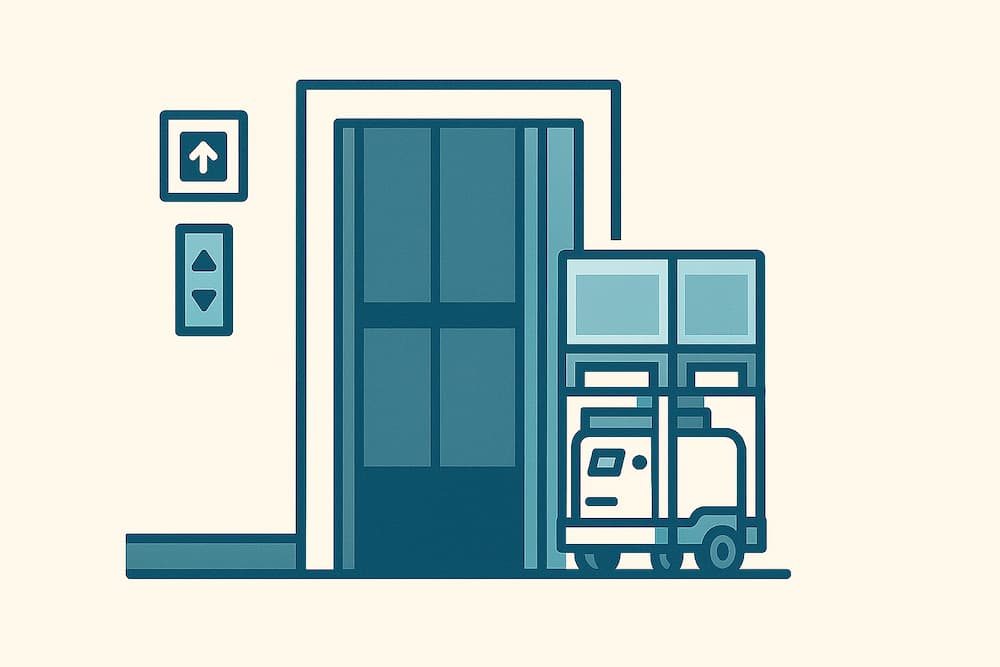
建屋が複数フロアに分かれている場合、AGV/AMRがエレベーターと連携して自動で階層を移動。エレベーターの呼び出し・搭乗・降車を制御する仕組みが求められます。
クリーンルーム内搬送
製薬・半導体業界など、微粒子対策が求められる現場に対応。静電気対策や低騒音・低振動設計、HEPAフィルター搭載など、清浄度を維持しながらの搬送を実現します。
冷蔵・冷凍ゾーン対応搬送
冷気や結露に強い防水・防寒仕様のAGV/AMRが使用されます。温度変化によるセンサー誤作動やバッテリー劣化を防ぐための設計が重要。食品・医薬品物流に活用されます。
防爆環境対応搬送
可燃性ガスや粉塵のある危険エリア向けに、電気系統やモーターの防爆構造を備えた特殊なAGV/AMRが活躍。化学工場などでの安全な無人搬送に対応します。
人との協働パターン別
人が置いた荷物を搬送
作業者が決まった場所に荷物を置くと、AGV/AMRが自動で回収・搬送。作業者の移動を削減でき、省人化と効率化を両立。シンプルな運用で導入ハードルが低い点も利点です。
人と同じ通路を走行
作業員とAGV/AMRが同じエリア・通路を共有する場合、LiDARやカメラによる障害物検知と減速・停止機能が不可欠。協働環境でも安全性を確保できる設計が求められます。
ピッキングアシスト型
棚搬送型のAGV/AMRが、ピッキング作業者のもとへ対象棚を移動させる「Goods-to-Person」方式。作業者の移動を最小化し、1人あたりの処理能力を大幅に高めます。
用途の特殊性による分類
工程間バッファ調整搬送
製造ラインで発生する工程間の待ち時間や在庫過多を防ぐため、仕掛品の一時保管・分配搬送を行います。過不足なくラインに供給し、ボトルネック解消に寄与します。
ジャストインタイム(JIT)搬送
必要なモノを必要なタイミングで供給するJIT搬送に対応。生産計画と連携し、リアルタイムでの指示に基づいて搬送を最適化し、在庫削減とライン安定化を実現します。
製品出荷前の自動仮置き整列
出荷前に完成品をバッファエリアに整列搬送する用途。ロット順や出荷順に自動で整列されることで、出荷作業の段取りが効率化され、ミス防止にもつながります。
混流ライン対応搬送(多品種搬送)
異なる品種や仕様の商品を1ラインで製造する混流生産に対応。AGV/AMRが品番や工程に応じて搬送内容を切り替えることで、柔軟なライン構築が可能になります。
夜間・無人稼働時の搬送
人が不在の夜間や休日でも稼働する無人化モデル。自動充電や自律走行機能を備え、24時間体制での連続稼働が可能。生産性向上と人件費削減の両立を支援します。
まとめ
AGV/AMRの活用事例を通じて、工場や物流現場での効率化や安全性向上の可能性について具体的なイメージを持つことができたでしょうか。AGV/AMRの導入を検討している方の多くは、コスト削減や作業効率の向上、人手不足の解消といった課題をお持ちかもしれません。今回紹介した事例が、そうした課題解決のヒントとなれば幸いです。
AGV/AMRの具体的な導入方法を検討される場合は、こちらの記事「AGV/AMRの導入方法|ステップバイステップガイド」も参考にしてみてください。
PhoxterのAGV/AMRソリューション
Phoxterは、工場や物流倉庫に対して自動搬送ロボットを用いた自動化・省人化ソリューションを提供しており、2,000台以上の導入実績があります。Phoxterでは、現場環境や業務フローを詳細に分析し、導入・運用コスト、効率性、柔軟性といった要因を総合的に評価し、最も効果的なソリューションを提案することができます。
AGV/AMRの導入や、工場・物流施設の自動化をお考えの方は、ぜひPhoxterにお問い合わせください。