2025年2月12日更新
鋳造時に発生するひけ巣をはじめとする欠陥・不良の検査方法を効率化したいニーズは強く存在しますが、従来の手作業や機械による検査方法ではどうしても時間がかかり、また精度が不十分な場合も頻繁にあります。そこで、これらの鋳物製品の検査方法に関する課題を解決するため、最新の画像認識技術が注目されています。
本記事では、ひけ巣やブローホールなど欠陥・不良の種類、鋳物の検査に用いられる様々な方法、さらには画像認識による外観検査のメリット・デメリットまでをわかりやすく解説します。具体的な検査方法や検討ポイントについて知りたい方は、ぜひご一読ください。鋳物の品質向上と作業効率化に役立つ情報をお届けします。
本記事は、画像処理アルゴリズムを活用してAI外観検査システムを自社開発し提供している株式会社Phoxterが作成しています。(Phoxterの外観検査自動化ソリューションはこちら)
鋳物に発生する不良5種類の解説
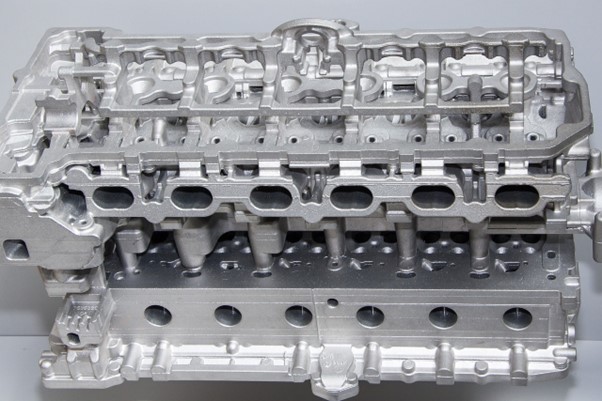
鋳物で発生する5つの不良について解説します。
ひけ巣
「ひけ巣」とは、鋳造された金属内に形成される空洞のことです。これは、鋳造工程における一種の欠陥であり、特に代表的なものの一つです。
ひけ巣は、溶融金属が凝固する際の収縮によって生じます。具体的には、溶湯が鋳型内で冷却されると、まず液体収縮が起こります。その後、凝固が進むにつれて固体収縮が発生します。この過程で、溶湯が固体になる際に体積が減少し、その不足分を補うために溶湯が供給されます。しかし、凝固が進むにつれて溶湯の供給が不足し、空洞が形成されることになります。
この空洞が生じる部分は耐久性が低下し、金属の弱点となります。その結果、製品の品質が低下し、信頼性や耐久性に影響を及ぼす可能性があります。
ブローホール・ピンホール
「ブローホール」とは、鋳造時に金属製品内部に形成される空洞のことです。この欠陥は、鋳造プロセス中に溶融金属に空気やガスが混入することで生じます。
ブローホールは、鋳造製品における最も一般的な欠陥の一つです。その発生原因は、主に以下の要因によるものです。まず、原料となる金属中から発生するガスや、溶融金属を流し込む際に湯口から混入する空気やガス、そして鋳型からのガスの放出などが挙げられます。
ひけ巣とブローホールは類似点がありますが、発生原因が異なるため、それぞれに対する対策も異なります。
割れ
「割れ」とは、鋳物が凝固する際に発生する欠陥の一つです。
鋳物は凝固時に収縮する性質があり、特に肉厚に差がある場合やピン角の部位では、収縮時に割れが発生することがあります。
湯まわり不良
「湯まわり不良」、または「ショート」や「外引け巣」「湯じわ」とも呼ばれる欠陥は、溶かした金属(溶湯)を鋳型に注ぎ込む際に、金属が隅々まで行き渡らずに凝固してしまう状態を指します。
この欠陥の主な原因は以下の通りです。
- 充填時間が長すぎること
- 鋳込み温度が低すぎること
- 鋳物形状の肉厚が均一化されていないこと
- 鋳型のガス抜きの設計が不適切であること
- 湯口形状や位置が不適当であること
- 溶湯量が不足していること
- 溶湯と鋳型との温度差が大きいこと
これらの要因が組み合わさると、溶湯が鋳型内で適切に流れないために湯まわり不良が発生し、製品の品質に悪影響を与える可能性があります。
ひずみ
「ひずみ」とは、鋳物形状がそりやねじれなどを生じることを指します。
金属を高温で溶かして成形する鋳造プロセスでは、部位や厚みによって冷却速度に違いが生じます。
具体的には、薄い部分は急速に冷える一方で、厚い部分や最終充填箇所は冷えるのに時間がかかります。
このため、冷えるのに時間がかかる内部が先に冷えた部分を引っ張ることになり、残留応力が生じます。
その結果、鋳物の形状が歪んだりねじれたりする現象が生じるのが「ひずみ」です。
9種類の鋳物の検査の解説
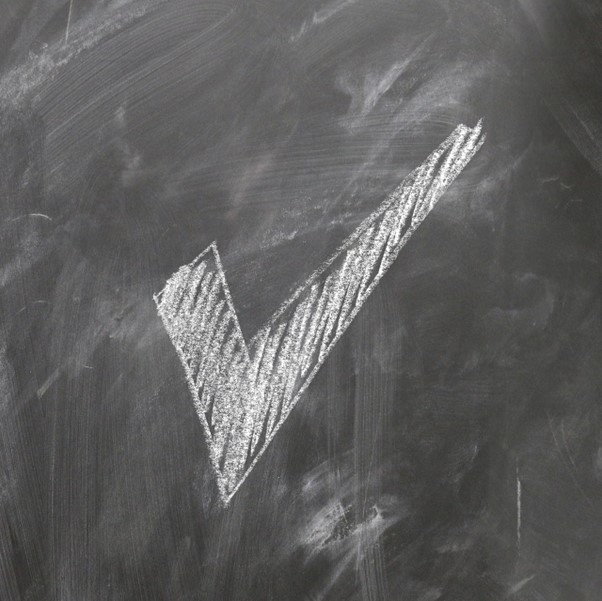
鋳物の検査に用いられる方法を解説します。
外観検査
鋳物の外観検査では、加工面や鋳肌面の表面状態を検査します。
対象となる欠陥には、外引け巣、キズ、打痕、亀裂、割れなどがあります。
以下に代表的な2種類の検査方法を挙げます。
深透探傷検査
「浸透探傷検査」は、表面に開口している欠陥に浸透液(着色浸透剤や蛍光浸透剤)を浸透させ、実際の傷よりも拡大した模様を形成させて肉眼で観察できるようにする方法です。
この検査方法は、主に鋳物表面の亀裂や気孔などの欠陥を検出するために用いられます。
磁粉試験
「磁粉試験」は、主に強磁性の材質に対して使用されます。
この検査法では、鋳物の表面に強磁性の粉末(磁粉)を塗布し、亀裂などの傷の部分に磁粉が吸着されて生じる模様を観察して欠陥を検出します。
この方法は、鋳物の表面に存在する傷や欠陥を検出するために効果的に使用されます。
形状検査・寸法検査
「寸法検査」では、従来のノギスやマイクロメーターを使った手動での測定方法に加えて、三次元測定機を用いた検査が広く採用されています。
さらに、複雑な形状の測定には、接触せずに計測が可能な3Dスキャナーの使用も普及しています。
引張強度試験
「引張試験」とは、材料の強度や伸びを評価するための試験手法です。
この方法では、試験片に徐々に張力を加え、材料が破断するまでの許容荷重と伸び量を精密に計測します。得られたデータから、その材料の引張強度や耐力が算出されます。
引張試験の手順や基準は、JIS(日本産業規格)によって定められています。
硬さ試験
「硬さ試験」は、金属部品の強度と耐久性を評価するために実施されます。
この試験では、ブリネル硬さ試験やロックウェル硬さ試験の方法が一般的に使用されます。
複数の箇所で硬さ試験を行うことで、材料の特性のばらつきを把握し、鋳物全体の品質の均一性を確保することが可能です。
硬度は、鋳物の摩耗、応力、衝撃に対する耐性を示す重要な指標の一つとされています。
X線検査
「X線検査」は、鋳物の内部欠陥を特定するために不可欠な技術です。
この検査では、鋳物材料を透過するX線やガンマ線を利用して、内部に存在する欠陥を可視化します。
作成される放射線画像を分析することで、引け巣、ボイド、亀裂などの様々な欠陥を検出することが可能です。
この方法により、材料の内部状態を正確に評価し、その品質を保証することができます。
超音波探傷検査
「超音波検査」は内部欠陥を発見するために広く採用されています。
この探傷検査法は、放射線検査に比べて安全性が高い点が特徴です。
超音波は物体内部で反射する性質を利用して欠陥を検出しますが、複雑な構造を持つ物体ではこの反射原理により適切な検査が難しい場合もあります。
そのため、検査対象の形状や材質によっては、他の検査方法との組み合わせが必要になることもあります。
化学成分(スペクトル)検査
「化学成分検査」では、鋳物材料の化学的組成を精密に判定するために発光分析装置が用いられます。
この検査における分析手法は、JISによって厳密に規定されています。このプロセスを通じて、材料が所定の品質基準を満たしているかを確認し、製品の信頼性と性能を保証します。
顕微鏡試験
「顕微鏡試験」は、鋳物の微細な組織構造を詳細に調査するために実施されます。
この試験では、専用に作製された試験片を顕微鏡下で観察し、金属固有の組織模様を明らかにします。
この模様から、鋳物の物理的・化学的性質を推測し、材料の品質や性能を評価することができます。
音響試験
「音響試験」は、物体をハンマーで軽く叩いた際に生じる音を分析することで、内部の欠陥や空洞を検出する非破壊検査法です。
この方法は、超音波検査などが適用困難な形状を持つ物体や、現場で迅速な検査が求められる場合に特に有効です。
しかし、音から欠陥を識別するこの技術は、官能に依存するため、検査員の経験と習熟度が極めて重要です。
画像による外観検査の特徴の解説
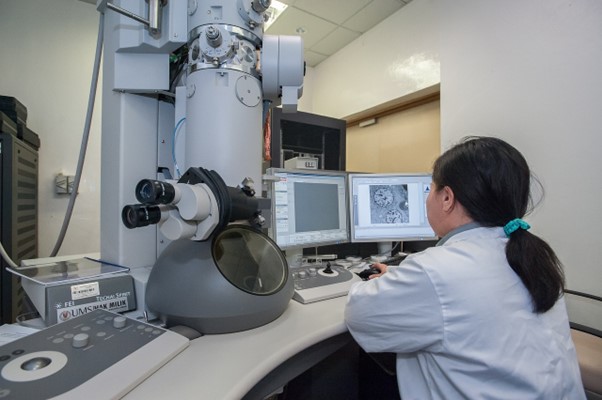
画像による外観検査を導入する際に知っておきたい事について解説します。
鋳物の検査への適用
画像認識技術の鋳物品質検査への応用により、欠陥の自動検出が実現しています。
この先進的な技術を活用することで、微細な亀裂や気泡のように、従来の検査方法では見過ごされがちな欠陥までをも確実に検出することが可能になります。
これにより、検査の精度と効率が大幅に向上します。
具体的には、外観検査、形状・寸法検査、顕微鏡検査、そしてX線画像検査において、画像認識技術を用いることで、人の介入によるばらつきが少なく、一貫性と高品質を兼ね備えた検査が可能になります。
従来の検査の課題
従来の手動検査や単純な機械を用いた検査方法は、効率的な生産体制にしばしば逆行します。
これには次の具体的な問題点があります。
- 検査精度の限界:手作業による検査は、熟練度や個人の判断基準によるばらつきが避けられず、特に微細な欠陥の見落としは顕著な課題です。
- 対応の遅れ:従来の検査方法では、結果を得るまでに時間がかかり、これが生産ラインの迅速な調整を阻害し、生産性の低下につながります。
画像検査の方式
産ラインに画像検査工程を組み込んだものを「インライン検査」、ラインから外れて検査を行うものを「オフライン検査」といいます。各特長を把握し、目的に応じた適切な方式を選択する必要があります。
以下に各方式の特徴を説明します。
インライン方式
生産ラインに検査工程を組み込んだ「インライン検査」は、全数検査がしやすく、生産性に優れます。
目視によるインライン検査は限界があるため、大量生産ラインについては画像検査を用いた自動化設備が用いられています。
次にインライン検査のメリット・デメリットを挙げます。
メリット | デメリット |
検査速度が早い | 自動化する場合は設備設計やライン設計が必要 |
自動化により全数検査可が可能 | 導入に技術的ハードルがある |
自動化により全数検査可が可能 | イニシャルコストがかかる |
自動化すれば人件費削減可能 |
オフライン方式
生産ラインとは別に検査工程を設ける「オフライン検査」は、精密な検査を実施しやすいが、運搬や計測などを手作業で行うため手間や時間がかかります。
次にオフライン検査のメリット・デメリットを挙げます。
メリット | デメリット |
精密な検査がしやすい | 目視(官能)検査の場合は、ばらつきが生じる恐れがある |
抜取検査が得意 | 全数検査が苦手 |
イニシャルコストを抑えられる | 目視(官能)検査の場合は、人件費がかかる |
画像検査による外観検査のメリット
一貫した検査基準
画像検査システムは、特定のアルゴリズムに基づき、一貫した基準で製品検査を実行する自動化技術です。
このシステムは、検査プロセスにおける人的要因による誤差を効果的に排除し、結果の再現性を大幅に高めます。
事前に定義された基準を用いて製品の品質を評価し、微細な欠陥や不具合を一貫して検出することができます。
これにより、品質管理の精度が向上し、生産ラインの効率と製品の信頼性が大幅に改善されます。
トレーサビリティ
画像検査システムは検査された製品の画像データを記録し、それを追跡可能にします。
このデータは品質保証や将来の参照のために重要であり、製造プロセスの透明性を高め、問題が発生した際の原因究明を容易にします。
効率化と時間短縮
画像検査システムは生産ラインにインラインに導入でき、連続して高速に製品を検査できます。このため、生産効率が大幅に向上します。
人手による検査に比べて時間を大幅に節約できます。
運用コスト
画像検査システムの自動化により、長期的には人件費の削減が期待できます。
微細な欠陥の検出
画像検査は、人の目では見逃しやすい微細な欠陥や小さな異物も検出できます。
これにより、品質の安定が期待できます。
画像検査による外観検査のデメリット
初期コスト
画像検査システムの導入には、カメラ、照明、コントローラーなどの機器に対する初期投資が伴います。
特に、インライン検査システムを生産ラインに組み込む場合、既存の生産ラインの再設計が必要になることも少なくありません。
システム導入の過程では、効果的な検査を実現するための教師データの蓄積、アルゴリズムの開発が必要です。
これらの準備作業には、充分な時間と注意深い計画が求められます。
従って、画像検査システムを生産ラインに導入する際には、慎重な計画と時間の確保が非常に重要となります。これにより、導入後の効果を最大化し、長期的には投資の回収と生産性の向上が期待できます。
システムの複雑さ
検査対象によっては、検査基準の設定やシステムの調整が特に複雑になることがあり、これらのプロセスは専門的な知識を必要とします。
特に、製品の形状が複雑であったり、検出すべき欠陥が微細であったりする場合、システムの精度を最大化するための調整が緻密に行われる必要があります。
その結果、運用開始までの準備期間が予想以上に長引くことも少なくありません。
このような状況では、専門知識を持つスタッフの確保や、必要に応じて外部の専門家との協力も考慮することが、効率的なシステム導入への鍵となります。
対応できない種類の欠陥がある
画像検査技術は、製品表面の欠陥を高精度で検出する強力な手段ですが、その能力には限界があります。
特に、製品の内部構造に生じた欠陥や、外観からは識別できない非可視的な問題の検出には適していません。このような場合、他の検査方法との組み合わせが必要となります。
例えば、内部欠陥の検出にはX線検査や超音波検査が有効であり、これらの方法は、製品内部の空洞や亀裂を可視化することができます。
画像検査とこれらの補完的検査技術を組み合わせることで、製品の表面的な欠陥だけでなく、内部の問題にも対応することが可能になり、全体としての品質管理体制の強化が実現します。
まとめ
本記事では、鋳物製品の外観検査における画像認識技術の採用に焦点を当て、その特徴とメリットについて考察しました。
従来の手動や機械検査と比べ、画像認識技術は検査の精度と速度を劇的に向上させます。
自動化によって一貫性のある検査基準を実現し、トレーサビリティを強化し、生産効率を顕著に改善するなど、多くの利点があります。
ただし、初期投資の高さやシステムの複雑性といった課題も存在します。
しかし、品質保証の基準が厳格化する現代の製造業界においては、画像認識を活用した外観検査の導入は必須の選択肢となっています。
適切な検査システムを選択し、その運用を始めるには、周到な計画と準備が欠かせません。
「画像検査の自動化を導入したいが、独力での進行に不安がある」とお考えの方は、Phoxterにご相談ください。
貴社のニーズに最適なソリューションを提案し、画像検査の導入に際して全面的なサポートを提供いたします。