製造業において、製品の品質を確保する外観検査は欠かせないプロセスです。しかし、従来の外観検査手法では限界を感じている企業も多いのではないでしょうか。この記事では、AIを活用し実際に効果のあった外観検査の導入事例を12例ご紹介します。これらの導入事例は、効率化や精度向上を実現し、実際の製造現場で大きな成果を上げています。AIによる外観検査の導入事例を通じて、どのように生産性を向上させ、コスト削減を実現できるのかを探ってみませんか?最新の技術を駆使した外観検査の導入事例を知ることで、あなたのビジネスにも新たな可能性が広がります。
なお、ここで紹介する導入事例は、全て株式会社Phoxterが手掛けたAI外観検査ソリューションです。より詳細な内容をお知りになりたい場合は、Phoxterまでお問合せください。
AI外観検査ソリューション導入事例
AI外観検査ソリューションの導入事例を12件ご紹介します。
導入事例1:アルミ包装
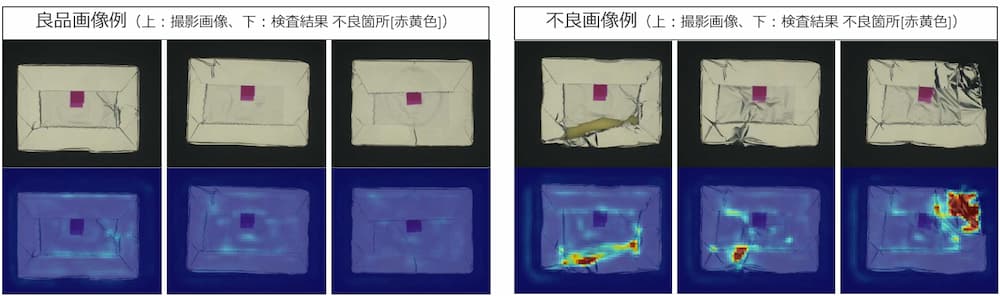
従来の外観検査の課題
- 良品状態のばらつきが大きく、不良箇所のみを適切に検出する画像処理アルゴリズムの構築が困難でした。
- 同種の不良モードでも発生箇所や程度により画像上での特徴の現れ方が変化しやすく、不良の安定検出が困難でした。
AI活用による解決策
- AIの活用により、従来のルールベース画像処理では困難だった不良箇所のみの高精度な検出が可能となりました。
- 良品状態の変化をAIが学習することで、過検出を極力抑えた柔軟な判定が実現し、過検出が改善されました。
導入システムと効果
- このシステムは、学習済みのAIモデルを用いて検査を実施できるため、開発工数を削減します。
- カメラ接続、設定画面、画像処理、AI外観検査、画像保存、Digital IO、PLCリンクなど、製造設備で求められる様々な機能をオールインワンで提供します。また、AI外観検査の前後に従来のルールベース画像処理を追加することも可能で、現場の要求に柔軟に対応できます。
導入事例2:ホイールナット内面
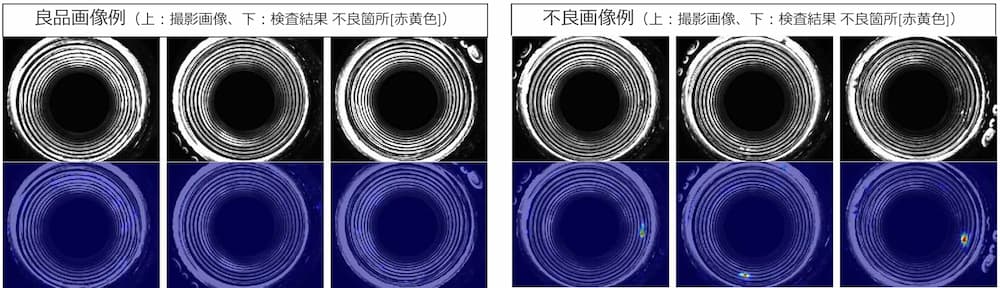
従来の外観検査の課題
- 照明の設置制約が大きく、画像上で全ての面が均一な明るさとなるように撮影することが困難でした。
- 製品形状による凹凸の影響で生じる陰影と不良を見分け、適切に判断するための検査アルゴリズム構築が困難でした。
- 同じような特徴を持つ不良でも、現れる場所により画像上での見え方が変化するため、安定検出が困難でした。
- 対象物を回転させて検査する場合、高精度な搬送機構とカメラの光軸・回転軸の厳密な調整が必要で、システム価格が高騰しがちでした。これらの要因により、過検出とシステム価格が課題となっていました。
AI活用による解決策
- AIの活用により、従来のルールベース画像処理では容易でなかった明るさが均一でない表面上の不良箇所のみを高精度に検出できるようになりました。
- 製品の詳細な位置決めや細かなマスク指定なしに検査を実施でき、過検出を改善します。
導入システムと効果
- 適切なレンズと照明を組み合わせることで、内面の360°を一度に撮影でき、対象物を回転させる機構が不要となり、システム価格を削減しました。
- このシステムは、AI外観検査を設備導入する上で追加のアプリケーション作成が不要であるため、開発工数を大幅に削減します。製造設備に必要な機能が包括的に提供されます。
導入事例3:包装の噛み込み
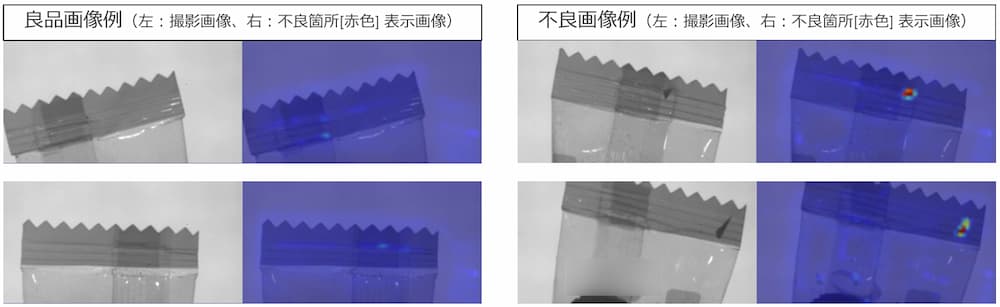
従来の外観検査の課題
- 包装の印刷があるため、可視光による撮影では欠陥箇所(噛み込み)の撮影が不可能でした。
- 印刷や包装の重なりの上にある欠陥を安定検出することが容易ではありませんでした。
- 対象物の撮影位置ずれや袋の状態が安定しないことにより、良品の画像上での見た目が変化し、過検出の原因となっていました。
AI活用による解決策
- 適切なカメラと照明の活用により、印刷を透過して欠陥箇所(噛み込み)を撮影することが可能となり、検査可能な画像が取得できました。
- AIは、検査対象の位置や袋の状態が異なる画像をまとめて学習し、従来のルールベース画像処理では困難だった印刷や包装の重なりの上に存在する欠陥箇所のみを高精度に検出可能にし、過検出を改善しました。
- 対象物の撮影位置ずれや袋の状態が多少変化した場合でも検査可能となり、過検出を抑制します。
導入システムと効果
- 学習済みのAIモデルを用いることでAI外観検査を実施可能で、追加のアプリケーション作成が不要であるため、開発工数を削減します。製造設備で求められる多様な機能をオールインワンで提供します。
- 特に、カメラと当社の画像処理コントローラーを組み合わせることで、可視光では検出できない欠陥も短期間でシステム構築し、検出可能となる特長があります。
導入事例4:透明フィルム包装の破れ・異物
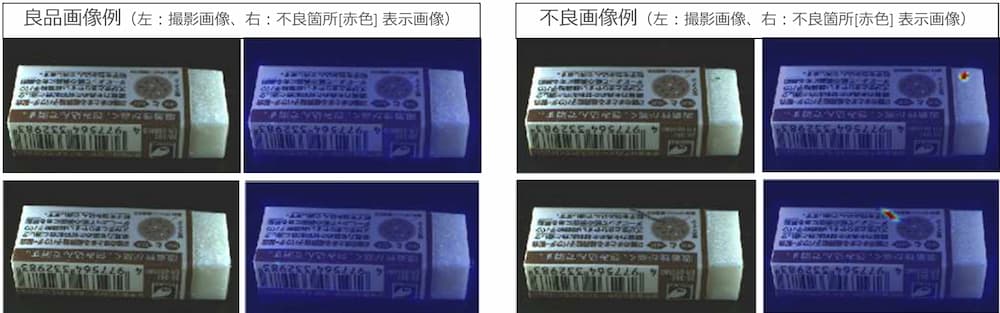
従来の外観検査の課題
- 透明フィルム包装において、印刷の上にある微細な破れや異物を安定して検出することが困難で、過検出が頻繁に発生していました。
- 対象物の撮影位置がわずかにずれるだけで、良品でも画像上では異なる見え方になり、誤検知の原因となっていました。
- 従来の検査では、各検査面に対して正面からの撮影が必要なため、カメラ台数が多くなり、高精度な搬送機器も必要となることから、システム価格が高騰しがちでした。
AI活用による解決策
- AIは、従来のルールベース画像処理では難しかった印刷上に存在する欠陥(フィルム破れ・異物)のみを高精度に識別することで、過検出を大幅に改善しました。
- 対象物の撮影位置や向きの多少のずれをAIが学習するため、搬送精度への要求を緩和し、これによりシステム価格の削減にも貢献しました。
導入システムと効果
- 光学系の工夫により、対象物の上側面と側面を1台のカメラで撮影して検査することを可能にし、システム全体のコスト削減に繋がっています。
- AIモデルを導入するだけで検査が実施できるため、開発工数を大幅に削減し、AI外観検査の導入に際して追加のアプリケーション開発が不要となる利点があります。また、AI外観検査の前後に従来のルールベース画像処理を組み合わせることで、現場の多様な要求に柔軟に対応可能です。
フィルムの外観検査については、こちらの記事「フィルム外観検査の方法を徹底解説!」で詳しく解説しています。
導入事例5:茶葉の異物
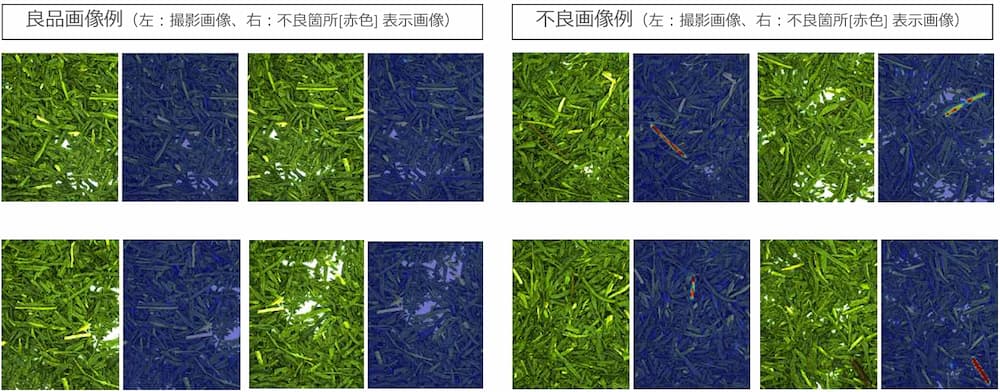
従来の外観検査の課題
- 対象物の形状、⾊味のばらつきが⼤きく、⽋陥箇所のみの検出が容易ではありませんでした。
- 比較的広い視野に対して細かな⽋陥の検出が必要で、高い分解能での撮影が必要となり、システム価格が高額になる傾向がありました。
AI活用による解決策
- AIの活用により、異物のみを高精度に識別し、過検出を改善することが可能となりました。
- 複数台のカメラを利用する場合でも、共通のAIモデルで検査できるため、開発工数を削減します。
導入システムと効果
- 学習済みのAIモデルを用いて検査を実施可能で、追加のアプリケーション作成が不要であるため、開発工数を削減します。製造設備で求められる多様な機能をオールインワンで提供します。
- AI検査の前後に必要に応じて従来のルールベース画像処理を追加することも可能で、現場の要求に対する柔軟な対応が可能となります。
導入事例6:金属部品の溶接ビード凹み
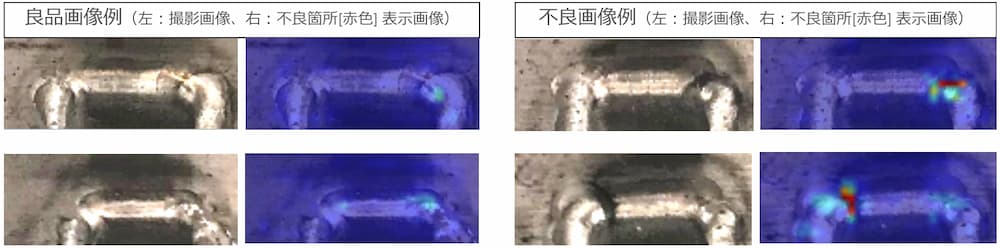
従来の外観検査の課題
- 金属部品の溶接ビードの外観検査では、良品であっても溶接部の形状や色味にばらつきがあるため、欠陥箇所のみを安定して検出することが困難であり、過検出が生じていました。
- 溶接ビードの位置や形状が一定でない場合、検査部位ごとに異なる欠陥検出アルゴリズムを作成する必要があり、開発工数が膨大になるという課題がありました。
- 一部の高度な外観検査では3次元計測カメラの導入が検討されることもあり、これがシステム価格の高騰を招くケースがありました。
AI活用による解決策
- AIは、溶接ビードの形状や色味の変動を許容しながら、欠陥箇所のみを的確に検出することで、過検出の問題を改善しました。
- 検査対象の状態が異なる画像に対しても単一のAIモデルで欠陥検出が可能であるため、検査部位ごとにプログラムを分ける必要がなく、開発工数の大幅な削減に貢献しました。
導入システムと効果
- 光学設計の工夫により、システム価格を抑えつつ、さまざまな対象物形状に一様の光を照射し、汎用性の高い検査を実現しています。
- AIモデルを導入するだけで検査が可能となるため、開発工数を大幅に削減でき、追加のアプリケーション開発も不要です。また、AI外観検査と従来のルールベース画像処理を柔軟に組み合わせることで、現場の複雑な要求にも対応できます。
溶接ビートのAI外観検査についてはこちらの記事「溶接ビード外観検査の基礎知識と事例:AI技術による自動化システムも紹介」で詳しく解説しています。
導入事例7:複雑形状の金属部品のキズ
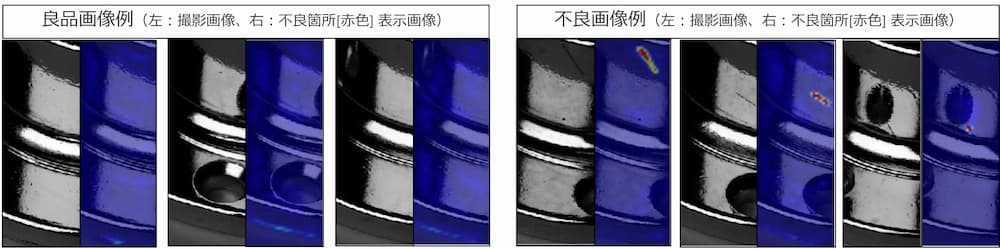
従来の外観検査の課題
- 対象物表面が異なる角度の平面と曲面から構成されており、画像上で全ての面が均一な明るさとなるように撮影することが困難でした。
- 同じような特徴を持つキズでも、不良が現れる場所により画像上での見え方が変化するため、安定検出を行うための検査アルゴリズムの構築が困難でした。
- 各平面を正面から撮影するようにカメラを設置した場合、カメラ台数が多数必要となる課題がありました。
- 対象物を回転させて全周を検査する場合、カメラの光軸と回転軸を厳密に一致させる必要がありました。
AI活用による解決策
- AIの活用により、従来のルールベース画像処理では困難だった、明るさが均一でない表面上の不良箇所のみを高精度に検出可能にし、過検出を改善しました。
- 製品の穴などをマスクすることなく外観検査を実施できるため、過検出を改善します。
- カメラ台数の削減と対象物の回転軸の調整負荷軽減を実現し、システム価格を削減します。
導入システムと効果
- 照明設計を工夫することで、設置制約が少なく、様々な表面形状に対応可能な汎用性の高い構成で検査能力を向上させています。
- 学習済みのAIモデルを用いて検査を実施可能で、追加のアプリケーション作成が不要であるため、開発工数を削減します。製造設備で求められる多様な機能をオールインワンで提供します。
金属部品の外観検査については、こちらの記事「金属部品外観検査の方法を徹底解説!」で詳しく解説しています。
導入事例8:透明樹脂製品(ペットボトル飲み口)
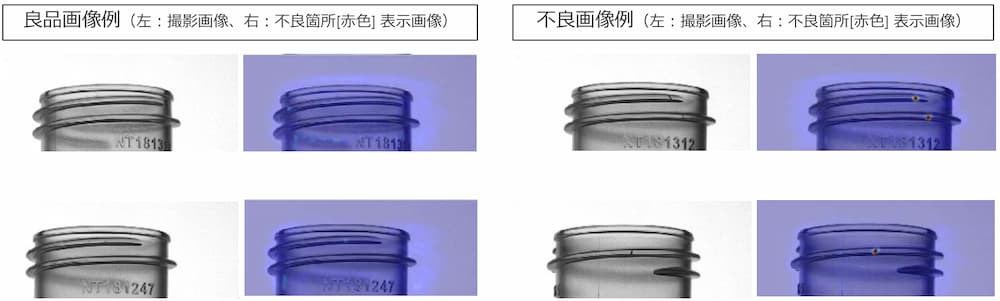
従来の外観検査の課題
- 対象物が透明で、かつ凹凸のある形状のため、欠陥箇所と陰影の切り分けが容易ではありませんでした。
- 撮影位置により対象物の形状(ネジ切りの位置、刻印の位置)が異なり、この変化を欠陥として誤検出してしまうことがありました。
- 対象物の撮影位置や回転ずれを抑制するために、高精度な搬送機器を導入する必要があり、システム価格が高騰してしまう課題がありました。
AI活用による解決策
- AIの活用により、従来のルールベース画像処理では困難だった、透明対象物の凹凸のある表面上に存在する欠陥箇所(キズ・汚れ)のみを高精度に検出可能にし、過検出を改善しました。
- 対象物の撮影位置や回転ずれによる画像上での見え方の変化をAIが学習するため、多少変化した場合でも検査可能となり、過検出の改善とシステム価格の改善に貢献しました。
- 4台のカメラで撮影した画像を全て1つのAIモデルで検査できるため、開発工数を削減します。
導入システムと効果
- カメラ4台を含む光学設計の工夫により、様々な対象物形状に一様の光を安定照射可能で汎用性が向上しました。
- 学習済みのAIモデルを用いて検査を実施可能で、追加のアプリケーション作成が不要であるため、開発工数を削減します。製造設備で求められる多様な機能をオールインワンで提供します。
ボトルのAI外観検査についてはこちらの記事「画像処理を導入したボトル外観検査の自動化ソリューション」で詳しく解説しています。
導入事例9:金属円筒製品の凹凸
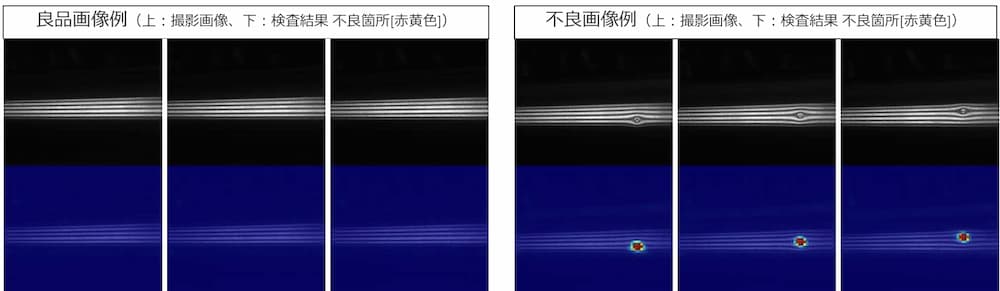
従来の外観検査の課題
- 一般的な照明環境では対象物表面の凹凸形状を画像上で取得することが容易ではなく、複雑形状の場合はさらに難易度が高くなりました。
- 特殊な照明環境を用いて凹凸情報を画像上で取得できたとしても、不良形状と位置により画像上での見え方が大きく変化してしまうため、その不良箇所のみを適切に検出できる画像処理アルゴリズムの構築が困難でした。
- 凹凸情報を取得するために3Dセンサを利用した場合、システム価格が高くなり、費用対効果が低下してしまう課題がありました。
AI活用による解決策
- AIの活用により、従来のルールベース画像処理では困難だった不良箇所のみの高精度な検出が可能となり、過検出を改善しました。
- 検査面の明るさに不均一さが生じた場合でも不良箇所の検出が可能となり、過検出を改善します。
導入システムと効果
- 光学系の工夫により、通常の照明環境では画像上で捉えることが難しい凹凸による変化を撮影可能にし、検査性能を向上させました。
- シンプルな機器構成で様々な対象物の検査面に安定照射可能で汎用性が向上しました。
- 学習済みのAIモデルを用いて検査を実施可能で、追加のアプリケーション作成が不要であるため、開発工数を削減します。製造設備で求められる多様な機能をオールインワンで提供します。
導入事例10:金属合わせ面の鋳巣
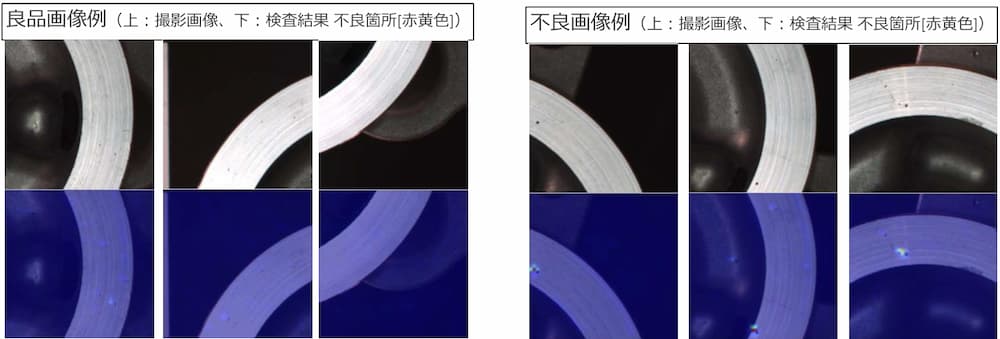
従来の外観検査の課題
- 製品上のヘアラインや汚れと不良(鋳巣)を見分け、適切に判断するための検査アルゴリズム構築が困難でした。
- 正常範囲の微細な鋳巣は検出せずに不良のみを適切に検出するための検査アルゴリズム構築が困難でした。
- 検査対象が大きくなる場合に、対象物全体を一度に撮影すると照明等の機材が大型化し、システム価格が高騰してしまう課題がありました。
AI活用による解決策
- AIの活用により、従来のルールベース画像処理では困難だった、表面上のヘアラインや汚れなどを避け、不良箇所のみを高精度に検出可能にし、過検出を改善しました。
- 検査面の明るさに不均一さが生じた場合でも不良箇所の検出が可能となり、過検出を改善しました。
- 対象物を分割して撮影した画像を1つのAIモデルで検査できるため、開発工数を削減します。
導入システムと効果
- 光学系機器構成の工夫により、様々な対象物の検査平面を均一に照射可能で汎用性が向上しました。
- 学習済みのAIモデルを用いて検査を実施可能で、追加のアプリケーション作成が不要であるため、開発工数を削減します。製造設備で求められる多様な機能をオールインワンで提供します。
鋳物に関する検査についてはこちらの記事「巣をはじめとする鋳物不良の検査方法と最新の検査動向」で詳しく解説しています。
導入事例11:鋳造部品(コンロッド・カムシャフトなど)
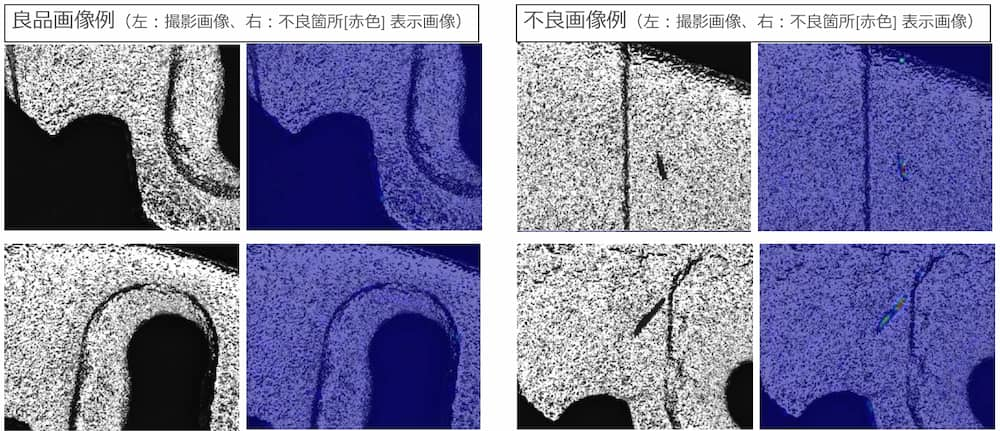
従来の外観検査の課題
- 良品箇所にも細かな凹凸が存在するため、欠陥箇所のみを安定検出することが容易ではありませんでした。
- 製品の構造上の凹凸部分と欠陥が連結した状態で現れた場合、欠陥のみを切り分けることが困難でした。
- 製品形状が複雑なため、1つの部品上でも検査箇所ごとに欠陥検出アルゴリズムの作成が必要となり、開発工数が課題でした。
- 3次元計測カメラを導入することによりシステム価格が高騰してしまうケースがありました。
AI活用による解決策
- AIの活用により、従来のルールベース画像処理では困難だった、鋳造部品表面の細かな凹凸部分や製品構造上の凹凸と欠陥を分けて検出し、欠陥箇所のみの高精度な検出が可能となり、過検出を改善しました。
- 撮影箇所の異なる画像に対しても1つのAIモデルで欠陥検出が可能であるため、撮影部位ごとにプログラムを分けずに1つのプログラムで検査可能となり、開発工数を削減します。
導入システムと効果
- 光学設計の工夫により、システム価格を抑えつつ、シンプルな機器構成で様々な対象物形状に一様の光を照射可能で汎用性が向上しました。
- 学習済みのAIモデルを用いて検査を実施可能で、追加のアプリケーション作成が不要であるため、開発工数を削減します。製造設備で求められる多様な機能をオールインワンで提供します。
導入事例12:黒地に黒い欠陥・白地に白い欠陥
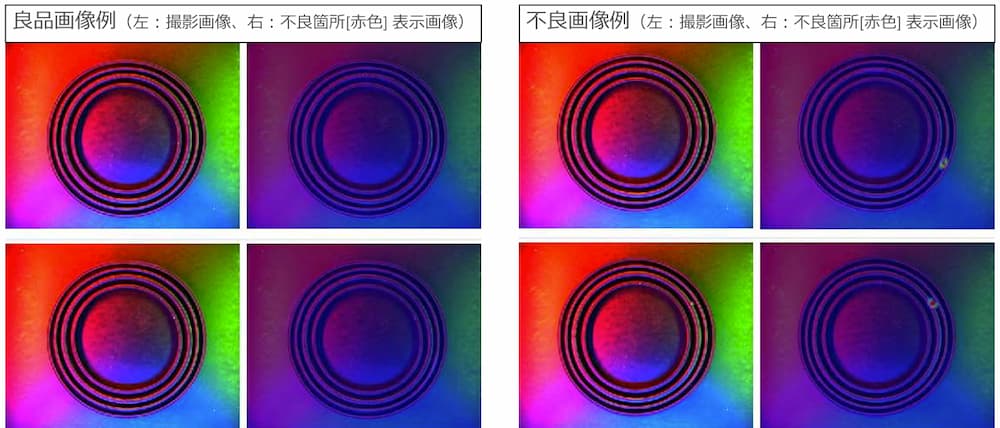
従来の外観検査の課題
- ピストンブーツ・ウェザーストリップなどのゴム製品の変形(湾曲)や表面の刻印の影響により、良品を不良と判定してしまうケースがあり、過検出が課題でした。
- 3次元計測カメラを導入することによりシステム価格が高騰してしまうケースがありました。
- 分割照明を用いて複数回撮影を行うことにより、検査タクトタイムが長くなってしまうケースがありました。
AI活用による解決策
- 画像上で欠陥箇所部分に色の乱れを発生させ、この色の乱れをAIが学習することで欠陥検出を実施します。
- 従来のルールベース画像処理では色の乱れを検出するしきい値設定が困難でしたが、AIの活用により色の乱れを検出する設定を容易に取得可能にし、過検出を改善しました。
- 必要な画像枚数が少なく、また不良箇所のアノテーション(塗りつぶし作業)が不要で、短期間に高精度な学習結果を取得可能にし、開発工数を削減します。
- 1回の撮影で検査が可能となるため、検査タクトタイムを改善します。
導入システムと効果
- 光学設計を工夫することで標準的なカメラ・照明の組み合わせ技術でシステムを構築できるため、システム価格を改善します。
- 学習済みのAIモデルを用いて検査を実施可能で、追加のアプリケーション作成が不要であるため、開発工数を削減します。製造設備で求められる多様な機能をオールインワンで提供します。
まとめ
ここまで12例の導入事例をご紹介してきましたが、当社のAI外観検査ソリューションを導入することで、以下のような共通した効果・メリットが得られます。
- 過検出の改善: AIを活用することにより、良品状態のばらつき、製品形状による陰影、印刷や重なりの上に存在する欠陥、表面の明るさの不均一さ、対象物の撮影位置ずれや変形といった要因によって生じる誤検出を大幅に抑制し、真の欠陥箇所のみを適切に検出することが可能になります。
- 開発工数の削減: 学習済みモデルをシステムにコピーするだけでAI外観検査が実施できるため、新たなアプリケーション開発が不要となり、開発工数を削減できます。また、検査対象の位置や向き、状態の異なる画像、あるいは複数台のカメラからの画像を一つの学習モデルでまとめて学習・検査できるため、検査部位ごとにプログラムを分ける必要がなく、開発効率が向上します。
- システム価格の改善/削減: 複雑な搬送機構や高価な3Dセンサーを不要とできるケースもあり、標準的またはシンプルなカメラと照明の組み合わせで検査システムを構築できるため、システム全体の導入コストを抑えることが可能です。少ないカメラ台数での検査実現もコスト削減に寄与します。
- 検査性能の向上:特殊なカメラや照明などの光学機器を組み合わせることで、可視光では捉えにくい印刷下の欠陥、または通常の照明環境では識別困難な微細な凹凸情報を画像上で明確に捉え、検査能力を向上させることができます。
- 汎用性の向上: シンプルな機器構成でありながら、対象物表面の反射を抑えたり、様々な形状の検査面に対して均一な光を安定して照射したりすることが可能であり、多様な対象物や複雑な表面形状の検査に幅広く対応できます。
- 製造現場の要求に対する柔軟な対応: 当社の画像処理コントローラーは、カメラ接続、設定画面、画像処理、AI外観検査、画像保存、Digital IO、PLCリンクといった製造設備に求められる機能をオールインワンで提供するハイブリッド型画像処理システムです。これにより、AI外観検査の前後に必要に応じて従来のルールベース画像処理を追加するなど、現場の具体的な要求に対して柔軟に対応することが可能です。
- 検査タクトタイムの改善: 従来の方式で複数回撮影が必要だったケースにおいても、AIを活用することで1回の撮影で検査を完結できるようになり、検査タクトタイムを短縮することが期待できます。
【もっと詳しく知りたい方へ】
当社のAI外観検査ソリューションは、ご紹介した事例以外にも、様々な製造現場の課題を解決しています。特に、今回の導入事例紹介では触れていませんが、カメラ・照明等の光学機器の選定もAI外観検査の成否に大きく影響するため、お客様ごとの環境に合わせた光学設計が必須です。
過検出の抑制、開発工数の削減、システムコストの最適化など、お客様の状況に応じた最適な解決策をご提案いたします。貴社の製品・工程に合わせた詳細な情報や、より具体的な導入事例については、ぜひお問い合わせください。